Concrete casting in cold weather and suitable admixtures for this condition
Introduction
When the temperature of the environment for concrete casting reaches below +5˚C or when the temperature is likely to reach lower than +5˚C during concrete curing, the cold weather condition is created. Therefore, it is necessary to comply with the concrete casting requirements in cold weather since cold weather affects concrete components and increases the possibility of mix water freezing (Which is not involved in the hydration reaction yet), as well as reduces the rate of gaining strength and therefore, threatens the quality of the structure. It is necessary to comply with the requirements of concrete casting in cold weather regarding that one-third of the months of the year have cold weather in Iran and concrete casting in cold seasons (At the end of Fall and the beginning of Winter) faces limitations. It is necessary to take the requirements for concrete casting in cold weather into consideration.
The following tips are suggested for concrete casting in cold weather:
Reducing the water-to-cement ratio in a constant cement content by using the plasticizer or superplasticizer admixtures.
Increasing the cement content
Using quick-setting materials and the accelerator of gaining strength (Quick-setting and quick-hardening)
Replacing type I and type II cement with Type III cement
Reducing the amount of natural pozzolans or replacing these pozzolans with artificial pozzolans or high pozzolanic activity in the mix design of the concrete
Increasing the temperature of fresh concrete in the required range by heating the components of the mixture.
The combination of some of the aforementioned methods or all of the above methods
Reducing the water-to-cement ratio by adding the superplasticizer admixture
The reduction in the water-to-cement ratio can improve concrete properties and concrete casting in cold weather in two ways:
Increasing the initial strength of the concrete and hence, reducing the curing period
Reducing the evaporable water in the concrete (The water that is not involved in the hydration) and hence, reducing the risk of freezing water inside the concrete pores.
The best way to reduce the mix water of concrete in cold weather is to use superplasticizer admixtures with no slow-setting material. The slow-setting material was used to produce most plasticizers and superplasticizers to give concrete the slump retention property. If the slow-setting material is not used, the fresh concrete will have a high slump decline and the opportunity to implement concrete will be reduced. On the other hand, the rate of gaining strength is reduced as well as, the first and second setting times of the concrete in case of using the slow-setting material. Therefore, concrete curing in cold weather is increased.
The Hamgerayan Production Company achieved the formulation of the Polycarboxylate Ether-based superplasticizers with slump retention property (SR Type) after conducting long-term research and development and incorporation with the concrete technical section of the Road, Housing & Urban Development Research Center. This company has produced the SR type superplasticizers with the CapcoCrete SRC prefix since 1400. It is noteworthy that this product has long-term slump retention (30 minutes to 3 hours) without using the slow-setting material. The CapcoCrete SRC4060 (Figure.1), CapcoCrete SRC5060 (Figure.2), etc. are some of the SR-type admixtures which are recommended for concrete casting in cold weather.
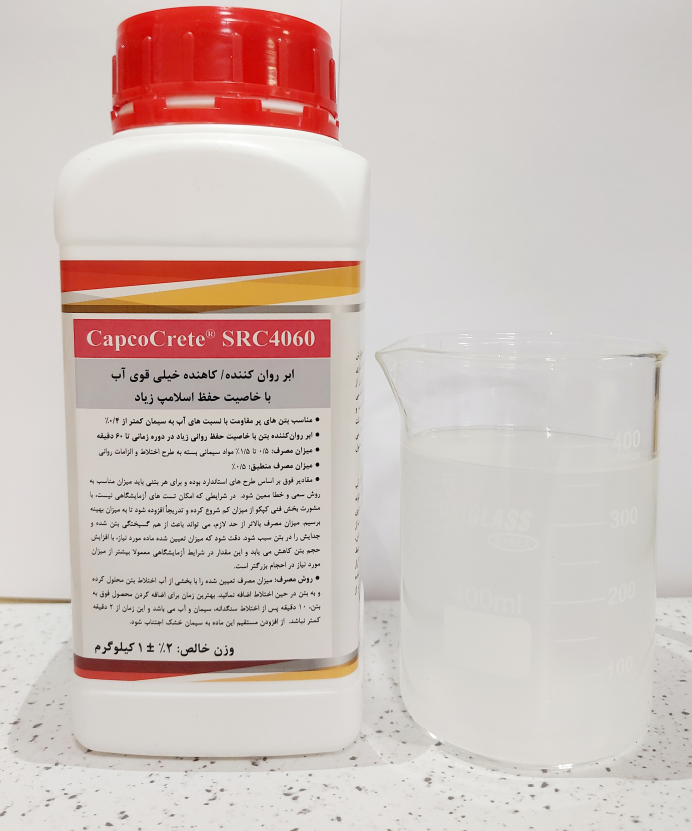
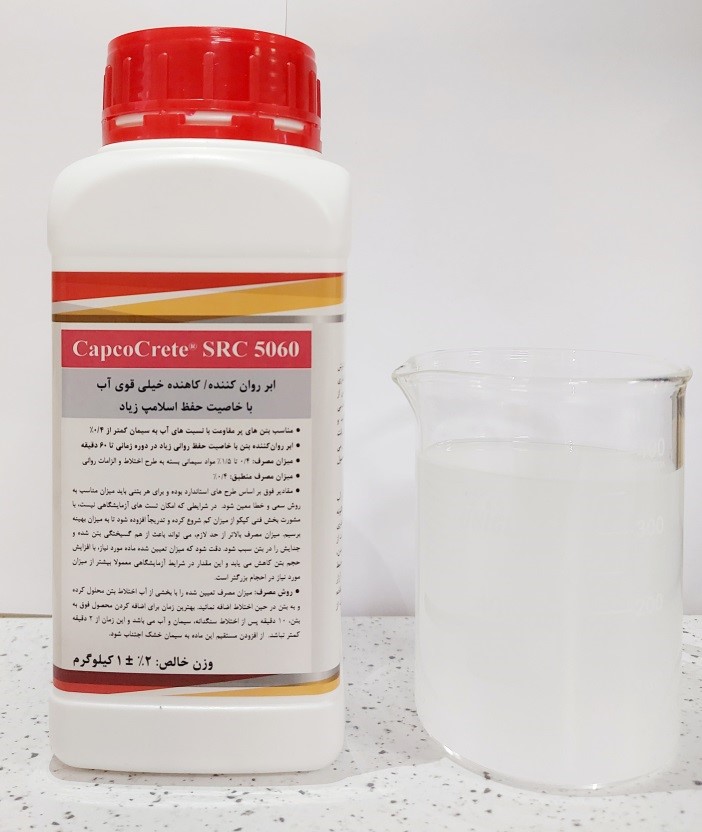
Increasing the cement content
Increasing the cement content can increase the produced heat in concrete at early ages. The rate of gaining strength is increased by increasing the concrete temperature at early ages and therefore, the curing period of the concrete in cold weather will be reduced. Moreover, increasing concrete temperature reduces the need for protective insulation.
Increasing cement content occurs in two ways:
Increasing cement content in a constant water-to-cement ratio: In this condition, merely increasing concrete temperature due to the hydration of a more volume of the cement can lead to a reduction in the curing period of the concrete. However, the constant water-to-cement ratio will not lead to an increase in the initial strength of the concrete.
Increasing cement content in constant mixing water: In this condition, both increasing concrete temperature due to the hydration of a more volume of the cement (therefore increasing the rate of gaining strength) and reducing the water-to-cement ratio (and consequently increasing the initial strength of the concrete) lead to a reduction in the curing period.
Using the quick setting and gaining strength material (Quick-setting and quick-hardening material)
These admixtures increase the rate of gaining the initial strength and therefore reduce the period of concrete curing in cold weather. This is a conventional method for concrete casting in cold weather and is commonly used in most of the cold regions of Iran.
It should be noted that the accelerators must not be used as a product for suitable curing and protection against concrete freezing since these materials do not significantly degrade the freezing point of water and are merely used to reduce the curing period of the concrete. The CapcoSet NCL (Figure.3) is supplied as a quick-setting material by the Hamgerayan Company. In 1399, this product has received a technical certificate from the Road, Housing & Urban Development Research Center which indicates an acceptable quality and proper performance of the product. The most important advantages of this product are as follows:
- Accelerating the initial and final setting time of the concrete
- Increasing the short-term compressive strength, in particular, the one-day compressive strength of the concrete, therefore, reducing the curing period in cold weather
- Increasing the initial temperature of the concrete due to intensifying the hydration reaction rate
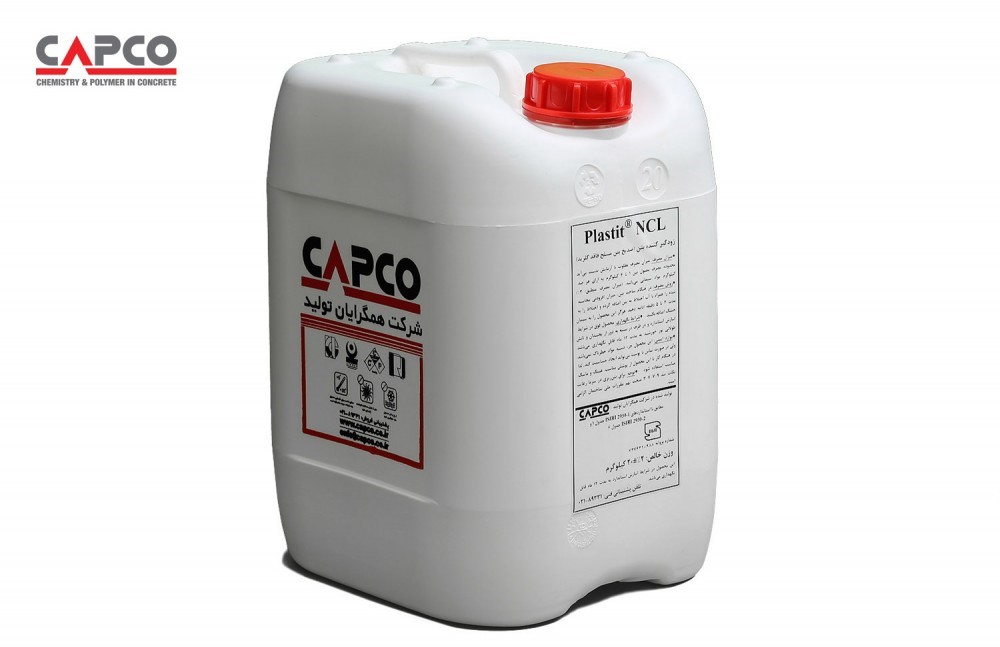
Replacing Type 1 and Type 2 cement with Type 3 cement
Generally replacing type 1 and type 2 cement with type 3 cement leads to an increase in the initial temperature of the hydration and the rate of gaining the initial strength of the concrete. Hence, the curing period of the concrete will be reduced.
Reducing the amount of natural pozzolans
In general, the natural pozzolans between 15% to 50% of the cement can produce heat in the hydration reaction. On the other hand, they do not contribute to gaining strength within the curing period with respect to the low percentage of pozzolanic activity at early ages. Therefore, it is recommended not to use pozzolans with low pozzolanic activity for concrete casting in cold weather or reduce their amount as much as possible. If these pozzolans are to be replaced, It is better to use artificial pozzolans with high pozzolanic activity like silica fume in the concrete mix design.
Increasing the temperature of the fresh concrete
Complying with the temperature range is one of the requirements of concrete casting in cold weather. Regarding the low temperature of concrete components in cold weather, it is necessary to provide the minimum temperature of fresh concrete. In most cases, heating the mix water using thermal systems and warming the coarse aggregates by using hot water tubes or using hot water steam, are some approaches to increase the temperature of the fresh concrete.