The use of admixtures in sustainable development
In the construction industry, concrete is the material that has been widely used by engineers and contractors due to its significant merits over other building materials. Obtaining the various physical and chemical properties of this material by adjusting the mix design and using different admixtures has made it possible to use this material for different usages under different environmental and chemical conditions. Moreover, the primary materials to make concrete are available and cheap.
With the advances in the urban planning and construction industry, different concrete admixtures with various usages appeared to improve the mechanical properties and the properties related to the concrete durability and fresh or hardened mortar. The use of these admixtures that can have a mineral or organic base has been significantly effective in providing the construction bed and developing megastructures, high-rise buildings, structures under high temperatures like furnaces, structures in contact with destructive materials like sewage, hydraulic structures, dam construction, and structures built in harbors or sea corrosive environments in contact with ions and different salts.
Different admixtures
The mineral admixtures include two natural categories such as Metakaolin, Zeolite, Truss, etc., and/or artificial pozzolans such as fly ash, Silica fume, etc. The design of chemical admixture is accomplished for the simultaneous enhancement of one or some properties of fresh concrete like self-compaction or self-leveling concrete or properties of hardened concrete like high strength or high-performance concrete. On the other hand, different properties can be given to these combinations by designing various structures and this freedom of action made concrete superplasticizer and plasticizer the most commonly used chemical admixtures in the ready-to-use and pre-cast concrete industry. The consistency, consistency retaining, adjusting the setting time, resistance to clay interference, resistance to Sulfate ion interference, adjusting viscosity, preventing concrete shrinkage, plasticizer with entraining property or on the contrary resistance to producing excessive air, adjusting the rate of gaining strength at desired times and other various topics are the main focus of the research in Capco Company.
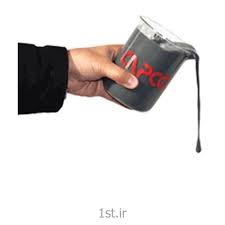
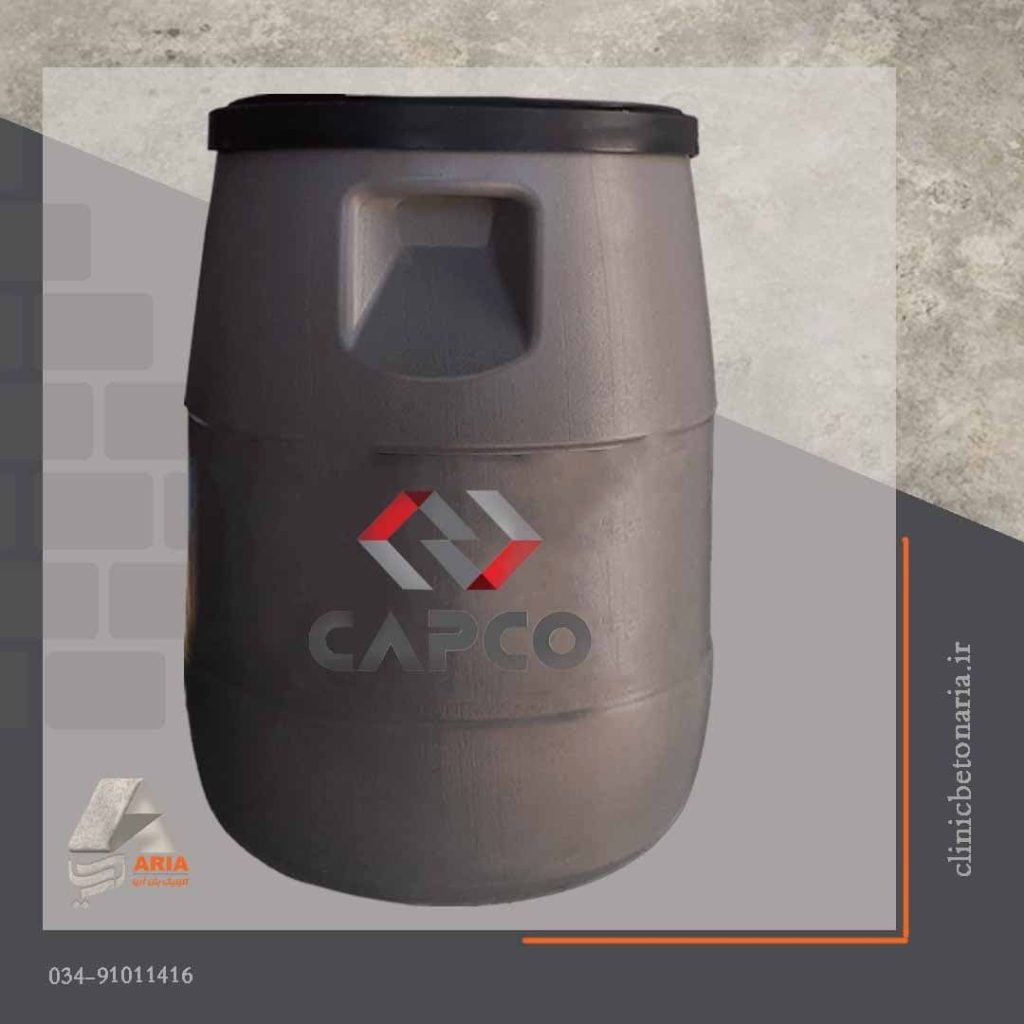
The plasticizer and superplasticizer
The evolution of plasticizers is accomplished based on the change in their chemical base. The concrete plasticizers of Capco Company are distributed with the trademark of CapcoPlast in the market which is suitable for concrete with a cement content of 350 and less. These materials are categorized based on consistency, temperature, and the desired slump retention. The CapcoPlast material is used between 0.4% and 2% by cement material weight. The accurate amount of CapcoPlast material is obtained by the test and trial method with respect to the properties of other materials such as sand and the current environmental condition. It is noteworthy that the excessive use of CapcoPlast by Capco specialists can decrease the consistency or delay the setting time of the cement. For higher cement contents, 350-400, the superplasticizer and super water-reducing admixture with the CapcoNorm trademark are used. The range of using these products is between 0.3% and 2% by weight of the cement material weight and the optimum dosage is obtained by the test and trial method as mentioned earlier.
The water-reducing admixture based on Poly Carboxylate Ether
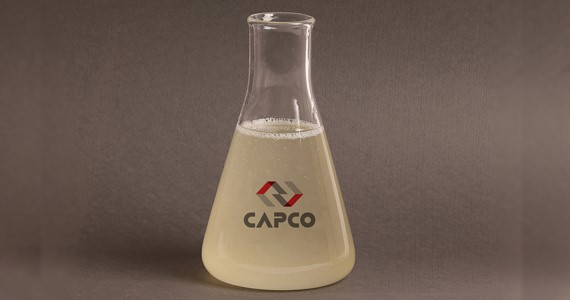
The use of admixtures in sustainable development
Besides the efforts that have been made to improve the quality of the concrete, the repair of concrete structures has also been taken into account to proceed with the objectives of sustainable development. The major damages reported for concrete structures are for the surface area. Engineers and researchers can consider two different approaches when facing these challenges- destruction and removing the damaged concrete and replacing it with new concrete and/or repairing the damaged surface of the concrete.
It is clear that the first approach i.e. removing the damaged concrete has received less attention than the second approach since it is time-consuming and it does not have any economic feasibility. Therefore, repairing the old damaged concrete surface seems to be more sensible and practical. However, the damage and its depth and whether the old concrete cross section is structural or not determine the final suitable repair method.
Concrete adhesive
The first question arising for any builder in the building construction industry is “What is concrete adhesive and where can it be used?”
Concrete adhesives refer to tiny organic polymer-suspended particles in the water that are commonly used in the construction industry.
The concrete adhesives are divided into two parts: in need of adhesion and need of water-proofing. The concrete adhesives are produced from Latex Polymers with Styrene Butadiene Rubber, Polyvinyl Acetate, Styrene Acrylate, and Resin Acrylate bases.
The mechanism of adhesive performance or latex is that the latex particles are accumulated in the pores when in contact with cement particles and water which are coagulated and changed into a polymer by removing water from hydration and evaporation.
Then the particles are concentrated and lead to forming a thin layer or so-called polymer film. Also, the bonding of cement particles and aggregates can be increased by the coagulation of latex and the filling of a part of pores by it. Concrete adhesives have many usages including:
- Bonding and connecting the old concrete with the new concrete
- Using mortars to repair honeycombed concrete
- Installation of tiles and ceramics in dry environments
- Curing concrete
- Improving the mortar durability
- Surface water-proofing
To bond the new concrete with the old concrete, the adhesive should be able to link the surfaces of the two elements and their chemical structure should have sufficient power to withstand the loads applied to this section. The concrete adhesive of the Hamgerayan Production Company (Capco) is produced with the CapcoBond trademark with different basics of Acrylic and Vinyl water-based resins the epoxy resins for repair applications with/without water-proofing properties.
The important note about using adhesives is when they are in contact with moisture. For instance, CapcoBond PVA and CapcoBond 121 are hydrolyzed in contact with moisture and lose their property. While CapcoBond AR and CapcoBond MO40 are based on Acrylic and are water-proof.
Moreover, CapcoBond EP is used for more particular and sensitive projects that require an adhesive with high mechanical and chemical strengths (High chemical strength against petroleum materials, seawater, oil, Ammonia, weak acids, etc. ) Bonding the old concrete to new concrete, concrete to metal and other materials, FRP coverage for retrofitting and covering different types of surfaces and making them impenetrable are other usages of EP adhesives.
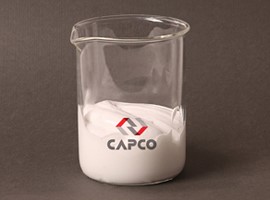
Rebar installation paste
The plan of a structure may require changing after a few months from implementation.
The rebar installation paste is the best product to add a layer of concrete to the main structure since the two structures should be linked and bonded together with a suitable mechanism and load transfer should be accomplished without rupture from the main structure.
The brief instruction to use the paste is that the holes are excavated by a drill and a round brush is rubbed inside the holes and the dust is removed from the surface of the hole by a strong blower. Then the installation paste is injected and the rebar installation is completed.
The rebar installation paste is generally supplied as two-component and three-component in the market. The rebar installation paste in Hamgerayan production Company (Capco) is known as the CapcoBond AS300 trademark. This is a three-component product and includes a powder part, a resin part, and a hardener part. The most important usages of this product are as follows:
- High adhesion to concrete surfaces
- High chemical resistance to petroleum materials, seawater, oil, ammonia, etc.
- High mechanical properties
- Without shrinkage
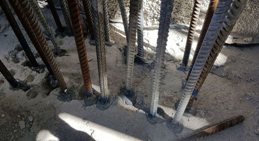